一体化自力式背压、减压、差压调节阀设计规范介绍了自力式背压调节阀的特性,分析了国内某核电站用辅助给水储罐直接作用式背压调节阀排量不足的原因,提出了将阀门更换为指挥器操作型背压调节阀的解决措施,并通过开启行程和流量系数试验,证明指挥器操作型背压调节阀满足工况要求。一种背压、减压、差压一体化自力式调节阀,包括阀体、阀芯,阀芯两侧的阀体之间通过导压管连通,导压管的中部设有就地压差表,阀体上通过固定架固定有双作用气缸,阀芯的阀杆与所述双作用气缸的气缸推杆连接,双作用气缸的两个气室均通过支管与就地压差表两侧的导压管分别连接,就地压差表两侧的导压管上和支管上分别设有手动调节阀。缸杆上设有弹簧组件,双作用气缸的两个气室分别设有气缸通气阀。很好的解决了多种工况灵活处理应用的问题。节约了投资、节省了时间,操作简便。为工厂根据不同工况调整阀门设置提供了可能,节约了采购周期和成本,更能有效保证工厂运行。 1、一体化自力式背压、减压、差压调节阀设计规范概述 自力式压力调节阀是一种无需外来能源,依靠被测介质自身压力,按预先设定值,进行自动压力调节的控制装置,自力式压力调节阀在石化和电力辅助给水储罐氮封系统使用较为普遍。本文针对国内某核电辅助给水储罐氮封系统的自力式背压调节阀排量不足问题进行了分析,并提出了阀门换型的解决措施。自力式调节阀作为一种无需外来能源,依靠介质自身的温度、压力、流量来进行自动调节的仪表,具有测量、控制和调节的综合功能,尤其适用于无电源和气源的场合。减压式即为阀后取压,背压式即为阀前取压,传统自力式阀门因为采用单作用隔膜执行机构,一旦选定自力式阀门的形式,到现场需要调整的时候则只能重新订货或者更换阀芯或者执行机构,耽误工厂施工和生产的进度。  一体化自力式背压、减压、差压调节阀设计规范技术实现思路 本技术的目的是提供一种灵活性、多样性的背压、减压、差压一体化自力式调节阀。本技术的目的是通过以下技术方案实现的:本技术的背压、减压、差压一体化自力式调节阀,包括阀体、阀芯,其特征在于,所述阀芯两侧的阀体之间通过导压管连通,所述导压管的中部设有就地压差表,所述阀体上通过固定架固定有双作用气缸,所述阀芯的阀杆与所述双作用气缸的气缸推杆连接,所述双作用气缸的两个气室均通过支管与所述就地压差表两侧的导压管分别连接,所述就地压差表两侧的导压管上和支管上分别设有手动调节阀。由上述本技术提供的技术方案可以看出,本技术实施例提供的的背压、减压、差压一体化自力式调节阀,很好的解决了多种工况灵活处理应用的问题。节约了投资、节省了时间,操作简便。为工厂根据不同工况调整阀门设置提供了可能,节约了采购周期和成本,更能有效保证工厂运行。附图说明图1为本技术实施例提供的背压、减压、差压一体化自力式调节阀的结构示意图;图2为本技术实施例中弹簧的结构示意图
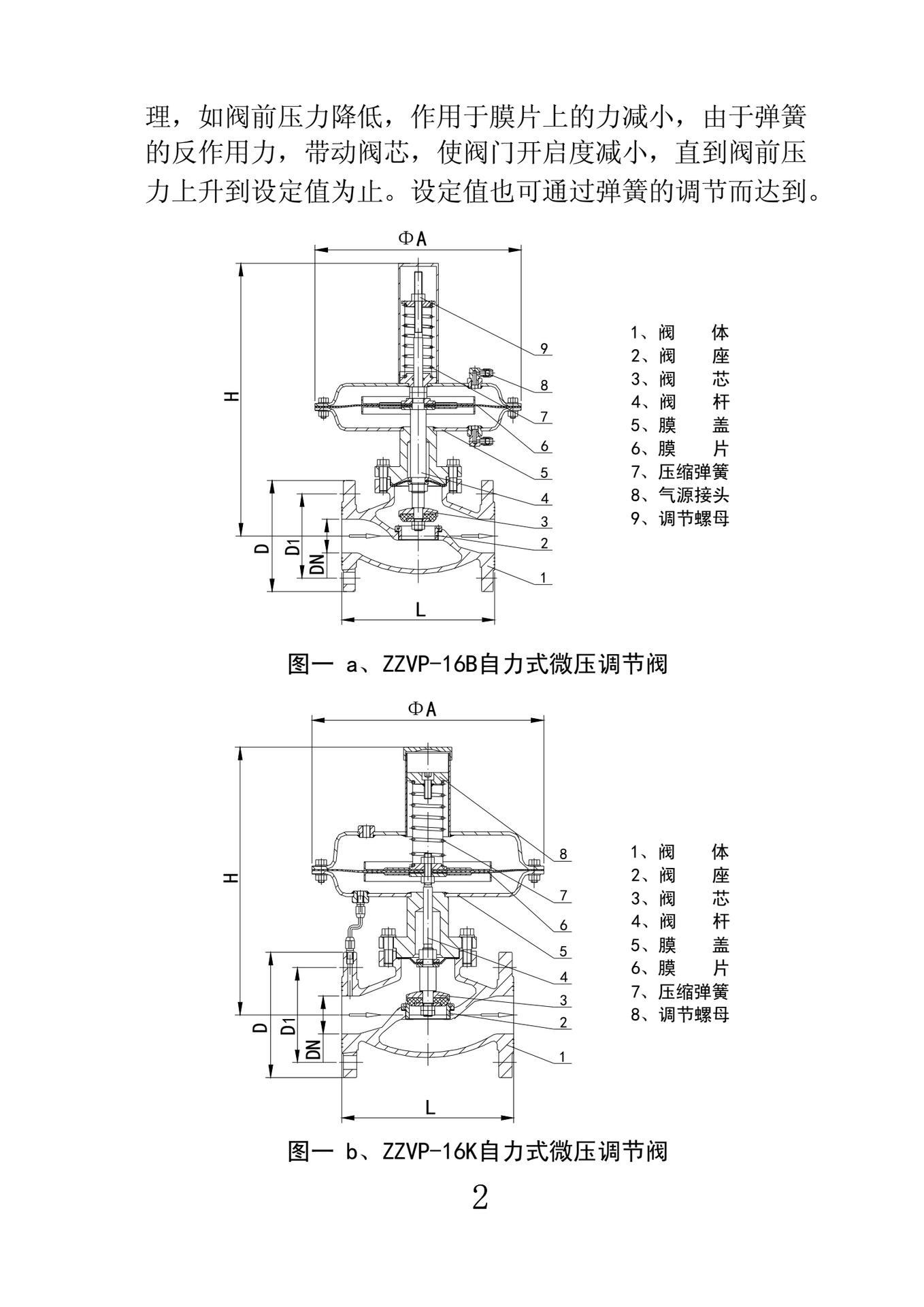 2、一体化自力式背压、减压、差压调节阀设计规范工作原理 核电辅助给水系统的给水储罐储存除盐除氧水,水上部采用氮气封闭以保护水不受空气的污染。储罐的氮封系统(图1) 包括进气和排气两部分。进气部分主要装置包括1个自力式减压阀和1个手动隔离阀,排气部分主要装置包括1 个自力式背压调节阀和1个手动隔离阀。正常运行时,进气和排气管道的手动隔离阀保持开启,氮气从供给系统引入,经减压阀减压后供给储罐。储罐氮气压力要求稳定在10kPa(g) 左右。 当储罐充水或氮封系统减压阀失效时,储罐的压力会异常升高。为了防止储罐因超压而损坏,背压调节阀开启排放多余的氮气。背压调节阀的开启设定压力为12kPa(g) ,要求的大排量为316Nm3/h。在核电厂试验过程中,当储罐的充水速度为40t/h 时,储罐的高压报警装置( 报警设定值为13kPa(g) ) 被触发,这表明背压调节阀的排量达不到系统设计要求。
 3、一体化自力式背压、减压、差压调节阀设计规范原因分析 3.1、功能和结构 背压调节阀为介质直接作用型,气室膜片的取压孔设置在阀门内部(图2) 。系统正常运行时,阀门的气室弹簧预紧力大于作用在膜片上的介质压力,使得阀瓣压紧阀座,阀门保持关闭。当介质压力达到或超过设定压力时,膜片下方的介质压力能够克服弹簧的预紧力,使阀门开启。阀门的开度与阀门的超压成正比。自式压力调节阀无需外加能源,利用被调介质自身能量为动力源引入执行机构控制阀芯位置,改弯两端的压差和流量,使阀前(或阀后)压力稳定。具有动作灵敏,密封性好,压力设定点波动力小等优点,广泛应用于气体、液体及蒸汽介质减压稳压或泄压稳压的自动控制。 本系列产品有单座(ZZYP)、套筒(ZZYM)、双(ZZYN)、三种结构;执行机构有薄膜式、活塞式二种;作用型式有减压用阀后压力调节(B型)和泄压用阀前压力调节(K型)。产品公称压力等级有PN16、40、64;阀体口径范围DN20~300;泄漏量等级有II级、IV级和VI级三档;流量特性为快开;压力分段调节从15~2500Kpa。可按需要组合满足用户工况要求。
 直接作用型背压调节阀结构简单,外形尺寸小,不需要设置外部取压口,安装方便。但是,阀门设定压力精度不高,且在超压工况有频跳的现象。由于阀门膜片的取压孔位于阀腔内,当阀门开启并排放流量时,储罐至阀门入口,以及阀门入口至阀门中腔都有流动引起的压力损失,此处所取的压力低于储罐的压力,不利于阀门达到要求的开度。另外阀门采用流关型结构,阀门开启后介质的流动不利于维持阀门的开启。当阀门开启排放流量时,阀腔内部流动紊乱,压力脉动较大,膜片经受压力脉动会引起阀门颤振,容易引起膜片、阀杆及导向面损伤。阀门的阀瓣/阀座采用金属密封(堆焊司太立合金) ,密封性能差。
 3.2、一体化自力式背压、减压、差压调节阀设计规范水力计算 氮封系统中,背压调节阀与给水储罐中间安装有1个手动隔离阀、4 个弯头(3 个90°,1 个30°) 和4.1m 长的管道。经管路水力计算,在大工作温度(60℃) 下排放设计要求的大流量(316 Nm3/h)时,阀门上游管道的气体平均速度达到17.9m/s( 气体动压0.18kPa) ,从储罐到背压调节阀入口有0.73kPa 的压损,假定储罐内氮气压力达到报警压力13.0kPa(g) ,减去阀门上游的压损和气体动压(该动压不能利用) ,阀门入口静压仅为12.09kPa(g) ,阀门出口静压为0.72kPa(g) ( 该出口静压是用于克服下游排放管道的压损) 。 由于阀门入口至阀门中腔有一定压损,阀门中腔取压孔处的压力会低于阀门入口静压,即气室膜片接收到的压力会低于阀门入口静压12. 09kPa(g) 。按阀门设定压力12.0kPa(g) ,此时膜片接收到的超压小于0.09kPa (g ) ,不到设定压力的0.75%。经分析,阀门在如此小的超压下无法达到要求的排量。
 4、一体化自力式背压、减压、差压调节阀设计规范结语 相对于直接作用型背压调节阀,指挥器操作型背压调节阀具有控制精度高、密封性好、可防止频跳等优点,其性能满足核电厂的设计要求。一种背压、减压、差压一体化自力式调节阀,包括阀体、阀芯,其特征在于,所述阀芯两侧的阀体之间通过导压管连通,所述导压管的中部设有就地压差表,所述阀体上通过固定架固定有双作用气缸,所述阀芯的阀杆与所述双作用气缸的气缸推杆连接,所述双作用气缸的两个气室均通过支管与所述就地压差表两侧的导压管分别连接,所述就地压差表两侧的导压管上和支管上分别设有手动调节阀。 一种背压、减压、差压一体化自力式调节阀,包括阀体、阀芯,其特征在于,所述阀芯两侧的阀体之间通过导压管连通,所述导压管的中部设有就地压差表,所述阀体上通过固定架固定有双作用气缸,所述阀芯的阀杆与所述双作用气缸的气缸推杆连接,所述双作用气缸的两个气室均通过支管与所述就地压差表两侧的导压管分别连接,所述就地压差表两侧的导压管上和支管上分别设有手动调节阀。
|